vertical grinding millgrinding

Operational parameters affecting the vertical roller mill
2017.4.1 Vertical roller mills (VRM) have found applications mostly in cement grinding operations where they were used in raw meal and finish grinding stages and in power
More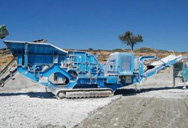
Grinding process within vertical roller mills: experiment and ...
2009.1.1 Based on screening analysis, laser size analysis, grindability and rigidity tests of samples collected on line from a cement and a power plant, a simulation of the
More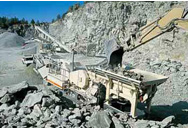
Predicting the grinding energy of vrm depending on material ...
2021.9.1 This study was aimed to create an alternative to determine the specific energy consumption of vertical roller mill grinding. The idea was to predict the grinding
More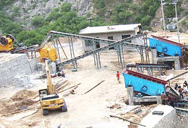
Detailed explanation of vertical mill grinding technology
Detailed explanation of vertical mill grinding technology Grinding technology has changed over the years, with vertical mills becoming even more popular. It has been proven that
More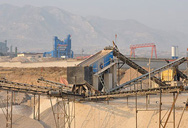
Grinding process optimization - IEEE Xplore
2017.6.19 The modular vertical roller mill for grinding cement raw material, cement clinker, and additives with an installed power of up to 12,000 kW was specifically
More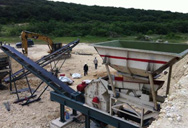
Research progress on control optimization of vertical roller
2022.11.23 Download Citation On Nov 23, 2022, Shuai Zou and others published Research progress on control optimization of vertical roller mill grinding system Find,
More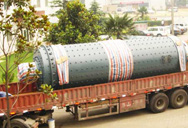
Operating experience with a vertical roller mill for
2012.3.1 Abstract Vertical roller mills are the mills traditionally used for processing granulated blastfurnace slag and for grinding composite cements. From the energy aspect they are superior to...
More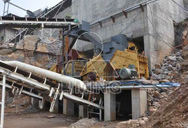
Chapter 14 Modeling Based on the Extreme Learning
2021.11.20 To address the problems in cement-grinding process production, the ELM is applied to model the process of raw cement vertical mill grinding, and the measured
More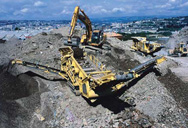
HIGmill high intensity grinding mill - Metso
Metso HIGmill™ - advanced and energy-efficient fine and ultra-fine grinding solution. The HIGmill™ comprises a mill body, shaft with grinding rotors, shell mounted stator rings, gearbox, and drive. The grinding chamber is
More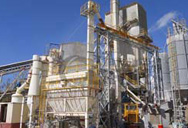
TOWER FINE MILLING EXPERIENCE AT MOUNT ISA
2016.6.3 The Tower mill is a vertical stirred grinding mill which can be used in both dry and wet grinding applications. It has provided a means of size reduction in an area
More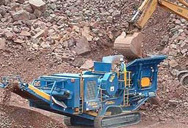
How to choose the right vertical sand mill horizontal sand
2023.1.9 1. The temperature of the slurry at the pre -scattered stage is not high, but once the horizontal sand mill began, the temperature of the slurry in the grinding cavity exceeds the protection temperature, so that the sand mill was stopped. In the case, we can appropriately increase the speed of the feed pump, thereby shortening the stay of the
More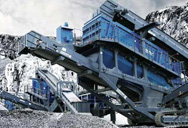
OK™ Raw and Cement Mill - FLSmidth
Our vertical roller mill offers optimum raw, cement and slag grinding. Our best-in-class OK™ Mill is a globally successful vertical roller mill solution for grinding raw material, cement and slag. Its cutting-edge design features consistently deliver the highest quality products with the greatest efficiency. It is affordable to install and ...
More
Vertical Grinding Mill (Coal Pulverizer) Explained
A vertical grinding mill consists of the following components: Electric Motor - to rotate the grinding table. The electric motor is often a three phase variable speed drive (VSD) induction motor, but designs vary. Reduction Gearbox
More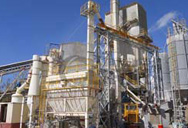
VXPmill for fine ultra fine grinding FLSmidth
The VXPmills are designed for fine and ultra fine grinding applications. In practice, the mill performs best when the feed has a normal distribution. However, the mill has been used to preferentially grind the coarser “hump” in bimodal distributions without over grinding the finer part of the distribution.
More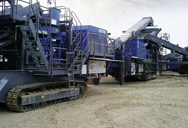
Roller Mill - Springer
2023.7.4 Roller mill is a type of grinding equipment for crushing materials by pressure between two or more rolling surfaces or between rolling grinding bodies (balls, rollers) and a track (plane, ring, and table). The roller mill with several grinding rollers as working components rolls along the grinding ring or the grinding table to crush the ...
More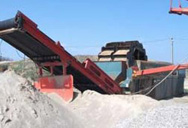
Review on vertical roller mill in cement industry its
2021.1.1 With the grinding capacity of a vertical roller mill and the ability to dry, grind and sort in a single unit, the vertical roller mill offers a definite advantage over the ball mill system [10]. A two-compartment ball mill with a highly efficient separator is still procured for new cement grinding units installation, although the vertical ...
More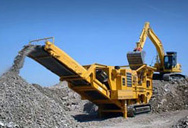
Coal mill, gypsum mill, clay mill, etc. Pfeiffer MPS mills
MPS 100 GC vertical roller mill for the grinding, drying and calcining of gypsum, Trevo, Brasil. MPS 3350 B mill for limestone grinding, China Chongqing Foreign Trade Huaneng, China. MPS 5000 B mill for raw material grinding, Turkey Tracim, Turkey. MPS 5300 B mill for cement raw material grinding, CDI Hail Cement, Saudi Arabia. Gebr. Pfeiffer SE.
More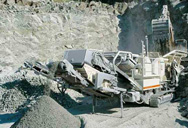
Energy-Efficient Technologies in Cement Grinding IntechOpen
2016.10.5 The energy consumption of the total grinding plant can be reduced by 20–30 % for cement clinker and 30–40 % for other raw materials. The overall grinding circuit efficiency and stability are improved. The maintenance cost of the ball mill is reduced as the lifetime of grinding media and partition grates is extended. 2.5.
More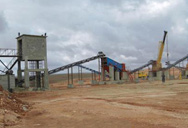
quadropol® - thyssenkrupp Polysius
In addition, the raw material grinding process will be supported by a QMR² 48/24. For the 4,000 tons per day kiln line Shiva Cement Ltd. contracted a quadropol® vertical roller mill for grinding pet coke with a QMK² 32/16. The same mill size QMK² 32/16 is running in Indonesia for years now, grinding and drying lignite.
More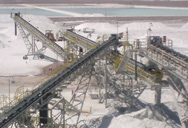
(PDF) A Comparative study on a vertical stirred mill agitator design ...
2015.7.16 This study focused on ultra-fine grinding of calcite powder (CaCO3) using a vertical stirred ball mill. The influences of various operating parameters such as stirrer speed (rpm), ball filling ...
More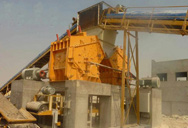
Vertical Super Fine Grinding Mill (Vertical Roller
Produk untuk Bidang Energy, Batu Bara, Listrik, Gas dan Minyak Bumi. by product information. Valve. Butterfly valves BT series; Reversing 4-way valves Model RVS
More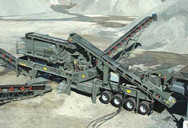
PROCESS OPTIMISATION FOR LOESCHE GRINDING
2017.8.12 The latest information about our over-seas companies is available on our homepage loesche. Loesche GmbH Hansaallee 243 40549 Düsseldorf, Germany Tel. +49 - 211 - 53 53 - 0 Fax +49 - 211 - 53 53 - 500. E-mail: loesche@loesche loesche.
More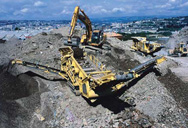
A discrete element method investigation within vertical
2022.9.1 The paper investigates the effects of changing the particle–particle restitution and sliding friction coefficients of grinding media within a vertical stirred mill using the discrete element method (DEM). A 190 mm diameter attritor mill containing 3491 particles was simulated to explore combinations of parameter values, across five
More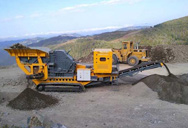
Operational parameters affecting the vertical roller mill
2017.4.1 Abstract. Vertical roller mills (VRM) have found applications mostly in cement grinding operations where they were used in raw meal and finish grinding stages and in power plants for coal grinding. The mill combines crushing, grinding, classification and if necessary drying operations in one unit and enables to decrease number of equipment
More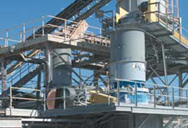
Mechanistic modeling and simulation of a batch vertical
2020.9.1 The present work experimental results were obtained from a previous study (Hasan, 2016), which consisted of batch grinding tests in a 2.2 kW batch vertical stirred mill, as shown in Fig. 1 (Hasan et al., 2017). A double-start steel screw with 200 mm diameter and 200 mm height was used as the stirrer. The clearance between the stirrer and mill ...
More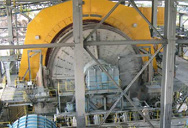
The Influence of Stirred Mill Orientation on Calcite Grinding
2021.4.21 Table 2 Grinding test conditions for both vertical and horizontal orientations. Full size table. The sample and grinding media were fed into the mill in the vertical position and then sealed and turned to the test orientation. The dry grinding tests were conducted as a batch type in which calcite samples were removed from the tank at
More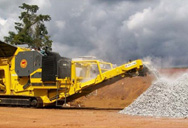
Vertical mill, Vertical grinding mill - All industrial manufacturers
wastewater mill UTN seriers. rotor double-roller vertical. Final grain size: 100 µm - 100 µm. Output: 60,000 kg/h - 480,000 kg/h. Motor power: 2,200, 4,000, 3,000 W. The Waste water Grinder from United Tech Machinery is a high torque, low rotating speed and double shaft grinder under water. It is designed to pulverizing all kinds of solid ...
More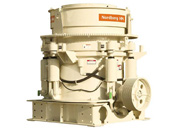
How to choose between ball mill and vertical roller mill?
2022.6.24 The vertical mill has high grinding efficiency and low energy consumption, and the power consumption is only 40%-50% of the ball mill. 7. Finished product quality. Compared with the ball mill, the product of the vertical mill has a higher degree of homogenization and higher purity.
More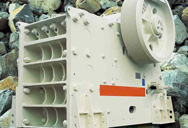
Polygonal concave wear and irregular packing behavior of grinding
2023.9.1 Grinding balls are an indispensable grinding medium in vertical grinding mills, grinding ore powder to target size. Some were severely worn and unrounded by iron ore from Anshan, China, during grinding operation in the vertical grinding mill (VTM-1500, Metso Outotec). Their service failure behavior was explored, based on classifying the
More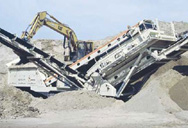
Predicting the effect of operating and design variables in grinding
2021.7.1 Grinding balls are an indispensable grinding medium in vertical grinding mills, grinding ore powder to target size. Some were severely worn and unrounded by iron ore from Anshan, China, during grinding operation in the vertical grinding mill (VTM-1500, Metso Outotec). Their service failure behavior was explored, based on classifying the
More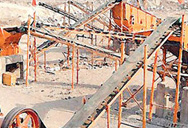
LUM Ultrafine Vertical Grinding Mill-SBM
2024.1.8 The ultrafine vertical grinding mill integrating ultrafine powder grinding, grading and transporting has become a better choice in the ultrafine powder grinding industry. Product Features: Higher capacity,
More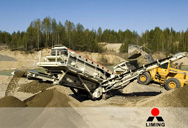
Open and closed circuit dry grinding of cement mill rejects
2004.1.14 A dry operated, horizontal stirred media mill was used for the fine grinding of limestone and compared in open and closed circuit modes. It was found that the choice of grinding aids as well as the stirrer tip speed are crucial for the mill operation, especially in terms of the grinding efficiency and the transport behavior through the mill.
More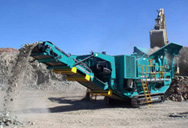
Grinding Mill - an overview ScienceDirect Topics
18.9.3 Grinding Mill Control in Closed Circuit. The principle objective for controlling grinding mill operation is to produce a product having an acceptable and constant size distribution at optimum cost. To achieve this objective an attempt is made to stabilize the operation by principally controlling the process variables.
More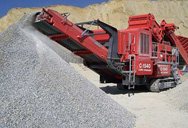
Regrinding and fine grinding technology - the facts and
2016.6.3 The fundamentals of fine grinding were established by Profesor Klaus Schonert in the 1980s and the fundamentals of stirred milling where developed in the 1980s and 1990s by German researchers, Steier, Schwedes, Stehr, Kwade and others. This work led to the development of a new generation of stirred mills capable of grinding finer and
More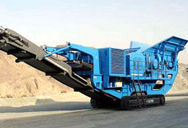
Vertical Roller Mill Wear Mechanisms and Preventive
2020.3.27 Using Vertical mill wear resistance material and learn the wear mechanism of the rolls and finding a method to improve its wear performance are important. This article shares the wear mechanism of ...
More
Review on vertical roller mill in cement industry its
2021.1.1 Vertical Roller Mills (VRM), High Pressure Grinding Rolls (HPGR), Vertical Shaft Impact Crushers (VSI) and more recently, Horizontal Roller Mill (Horomill) have saved the specific power by 45–70% when compared with a ball mill circuit [8], [10]. Now a days Ball mills and HPGR are installed together as a common unit.
More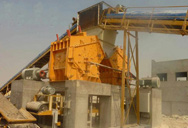
Minerals Free Full-Text Performance Comparison of the Vertical
2023.1.31 Varied types/geometries of stirred mills have been produced by different manufacturers, and the comparison task has been accomplished for some of the technologies, i.e., Tower mill vs IsaMill. However, the main drawbacks of these comparisons were the uncommon characteristics of the milling environment, such as media size. In
More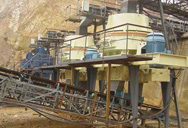
TOWER FINE MILLING EXPERIENCE AT MOUNT ISA
2016.6.3 Mount Isa Mines Ltd Mount Isa, Queensland 4825. Abstract -. Over the last ten years Tower mills were studied and used for regrinding and fine grinding applications at MIM operations. They were found to be more energy efficient than regrinding tumbling ball mills, more reliable, and easy to operate and maintain.
More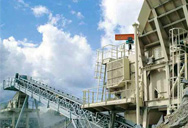
Analysis and Optimization of Grinding Performance of Vertical
2022.1.23 This work concentrates on the energy consumption and grinding energy efficiency of a laboratory vertical roller mill (VRM) under various operating parameters. For design of experiments (DOE), the response surface method (RSM) was employed with the VRM experiments to systematically investigate the influence of operating parameters on
MoreArticle aléatoire
- Broyeur agrave moulin agrave marteaux agrave vendre
- concasseur de roche compacte portable
- piedra de eje vertical trituradora de piedra de la maacutequina trituradora
- venta de chancadora de piedra en cusco
- la mâchoire de sertissage partie d impact de concasseur
- concasseur Indonésie marteaux de pierre de sable faire stone quarry
- concasseur à mâchoires alluminium
- rolloing moulin au bengale occidental
- LIMING 400 machine for sale
- fournisseur de machine de moulin
- les mines dor du mercure
- Processus De Afrique concasseur de Scories Dacier
- laver le sable usine a Dubaï
- ligne de production de matériaux de construction
- broyeur Indonésie Calcite de chaudière
- Machines De Nettoyage De Ballast
- de pierre de sable materiau qui en inde
- developmebt de la chine grâce aux exportations de charbon
- Laminoir Vertical Dans Les Cimenteries
- broyeur de pierres introdution
- rectifieuse de sol en pierre
- pour écraser la demande de calcaire
- kenya vendeurs de concasseurs de pierre utilises
- machines de moulin a farine fournisseurs
- piste de broyeur à béton
- comment identifier une pierre d'or de la minemarques
- Écraser les plantes de sable à hyderabad
- fabrication de briques
- technique de Calcite broyeur a boulets
- industrie directe Machine vilebrequin de broyage